Energiespeicher
Zurück zur Startseite Grüne Elektroautos
Probleme der Energiespeicher für die Elektromobilität
Eines der größten Probleme der Elektromobilität ist es, geeignete Energiespeicher zu entwickeln. Auf dem Stand der Technik 2013 kann aufgrund des hohen Gewichts leistungsstarker Akkus nicht genug Energie im Fahrzeug mitgeführt werden, um lange Strecken zu überwinden. Entgegen der Erwartungen hat aber der gesamte Produktlebenszyklus eines Lithium-Ionen-Akkus eine geringe negative Auswirkung auf die Ökobilanz des Elektrofahrzeugs.
Im Gegenteil dazu senkt der hohe Energieaufwand bei Herstellung und Speicherung von Wasserstoff für die Verwendung in Brennstoffzellen deren Ökobilanz drastisch. Unabhängig von der Technologie hat die Herkunft des Stroms eine ungleich höhere Auswirkung darauf, wie „grün“ Elektromobilität ist.
Möglichkeiten der Speicherung von Energie für die Elektromobilität
Heutzutage ist die gängigste Form Energie zu speichern der Akkumulator. Ein wichtiges Bewertungskriterium für Energiespeicher ist die spezifische Energiedichte/Leistungsdichte in der Einheit Energie in Wattstunden pro kg Gewicht (zum Vergleich mit Kraftstoffen siehe Alternative Kraftstoffe).
Ist gibt verschiedene Möglichkeiten Energie chemisch in einem Akku zu speichern. In der Vergangenheit ist vor allem der Bleiakkumulator als Starter- und Bordnetzakku von Bedeutung gewesen, da er kostengünstig ist, ein gutes Tieftemperaturverhalten hat und kurzfristig sehr hohe Entladeströme abgeben kann [1]. Sein Nachteil besteht aber darin, eine sehr geringe spezifische Energiedichte von 30 Wh/kg zu besitzen. Er ist somit zu schwer für die Verwendung als Antriebsakku.
Nach einer kurzen Phase der Verwendung von Nickel-Cadmium-Batterien, welche wegen ihrer Giftigkeit aus dem Wettbewerb ausschieden, und Nickel-Metallhybrid-Akkus, welche wegen des Memory-Effekts (Verminderung der nutzbaren Kapazität nach häufiger Teilentladung) nicht erfolgreich waren, zeichnet sich heute ab, dass der Lithium-Ionen-Akku die vielversprechendste Option ist [2].
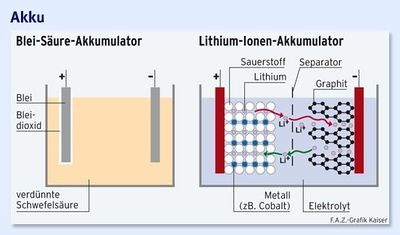
Der Lithium-Ionen-Akku besteht aus mehreren Sekundärzellen (Entladung ist reversibel). In diesen wird die elektrische Energie durch die Verschiebung von Lithium-Ionen gespeichert. Die positive Elektrode besteht aus Übergangsmetalloxid (z. Bsp. CoO2), die negative Elektrode häufig aus Graphit mit eingelagerten Lithium-Ionen. Die Lithium-Ionen können in einer Zelle durch das nicht wässrigen Elektrolyt zwischen den Elektroden hin- und herwandern [4]. Um die gewünschte Kapazität zu erhalten, werden viele Zellen verschaltet. Unter Einbeziehung der Verluste durch Verschaltung, etc., ergibt sich eine immer noch relativ hohe Energiedichte von 140 Wh/kg. Leider ist auch hier durch physikalische Grenzen kein sprunghafter Anstieg der Energiedichte zu erwarten. Die Schwerpunkte in der Forschung liegen momentan auf der Verbesserung der Verschaltung der Einzelzellen, der Sicherheit während aller Betriebsbedingung und der Industrialisierung der Fertigung zur Kostensenkung [5].
Die Anforderungen variieren je nach Einsatzort. Beispielsweise legen Amerika und China größeren Wert auf Sicherheit in Crash-Situationen und kostengünstige Herstellung, Europa aber auf ein möglichst geringes Gewicht. Dies ist auch begründet durch die verschiedenen Ausrichtungen in der Elektromobilität, wie zum Beispiel die Verwendung von Hybrid- oder reinen Elektroautos [6].
Zwei Systeme, die eine höhere Energiedichte besitzen, befinden sich momentan im Forschungsstadium: die Lithium-Schwefel-Zellchemie (ca. doppelte Energiedichte einer Lithium-Ionen-Batterie) und die Lithium-Luft-Zellchemie (3-4 fache Energiedichte) [7]. Bei beiden Konzepten ist aber noch nicht sicher, ob sie überhaupt funktionieren werden.
Herstellung, Nutzung und Entsorgung von Lithium-Ionen-Akkus
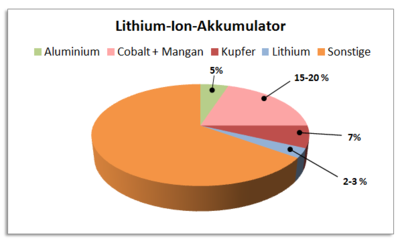
Es ist noch nicht vollständig erforscht, wie stark Herstellung, Nutzung und Entsorgung der elektrischen Energiespeicher die Umwelt belasten. Laut einer Studie der Empa (Eidgenössische Materialprüfungs- und Forschungsanstalt) ist der ökologische Fußabdruck von Lithium-Ionen-Akkus aber geringer als befürchtet. Die Studie zeigt, dass 15% der gesamten ökologischen Belastungen eines Elektroautos auf die Batterie entfallen. Die Hälfte entfällt dabei auf die Gewinnung der Rohstoffe Aluminium und Kupfer und ein noch kleinerer Anteil auf das Lithium. Insgesamt befanden die Forscher, dass der Strom-Mix ( siehe Strommix der Zukunft), mit dem die Batterie geladen wird, eine vielfach höheren Auswirkung auf die Ökobilanz des Elektroautos habe [9].
Bei der Rohstoff-Gewinnung sind auch soziale Folgen zu berücksichtigen (siehe Rohstoffe). Laut einer Studie des ZSW (Zentrum für Sonnenenergie und Wasserstoff-Forschung) ist bis mindestens 2050 weltweit ausreichend Lithium und Kupfer vorhanden, um die allgemeine Elektromobilität zu ermöglichen. Allerdings liegt ein Großteil der Lithium-Ressourcen in politisch instabilen Ländern wie Bolivien oder Chile. Es ist ersichtlich, dass dies Konflikte zur Folge haben kann, wie auch die Ausbeutung andere Ressourcen bereits nach sich zog. Auch aus diesem Grund wird bereits viel Energie in die Erforschung geeigneter Recycling-Verfahren gesteckt. Weitere bis jetzt weniger erforschte Rohstoffe für die Lithium-Ionen-Technologie sind Kobalt und Nickel [10].
Alternative Brennstoffzelle?
Im Sprachgebrauch wird Brennstoffzelle oft mit der Wasserstoff-Sauerstoff-Zelle gleichgesetzt. Sie ist die am besten erforschteste Art der Brennstoffzelle. Eine Wasserstoff-Sauerstoff-Brennzelle wandelt die chemische Reaktionsenergie des kontinuierlich zugeführten Brennstoffs Wasserstoff und des Oxidationsmittels Sauerstoff in elektrische Energie. Sie ist im eigentlichen Sinn kein Energiespeicher, sondern ein Energiewandler wie zum Beispiel auch eine Verbrennungskraftmaschine (VKM) [11]. Da der Wasserstoff aber nicht natürlich vorhanden ist wie Öl, muss er unter Energieaufwand erzeugt werden. Somit wird die Energie im Wasserstoff gespeichert und in der Brennstoffzelle gespeichert. Desweiteren wird die chemische Energie direkt in elektrische Energie umgewandelt und die in VKMs bei der Verbrennung und mechanischen Umwandlung entstehenden Verluste umgangen. Als Antrieb in Kombination mit einem Elektromotor ist sie somit theoretisch effizienter als ein Verbrenner, in der Praxis müssen jedoch alle Produktionsschritte mit einbezogen werden [12]. „Wird aus Strom Wasserstoff über Elektrolyse erzeugt, tritt dabei ein Verlust von etwa 40 % auf. Für den Transport und die Speicherung von Wasserstoff gehen weitere 10 % verloren. Die Brennstoffzelle im Fahrzeug hat einen Wirkungsgrad von maximal 50 % und der damit betriebene Elektromotor wieder einen Verlust von 10 %. Damit kann man nur 25 % der ursprünglichen Energie nutzen“ (Akkumulator: ca. 60%) [13].
Die Herstellung, die Speicherung und der Transport des Wasserstoffs senkt also die Effizienz der Brennstoffzelle drastisch und führt dazu, dass sie nicht viel ökologischer ist als ein Verbrenner. Dies ändert sich, wenn zur Herstellung des Wasserstoffs Strom aus erneuerbaren Energiequellen verwendet wird, besonders wenn eine Überproduktion von Strom ausgeglichen werden kann, wie sie oft durch Windparks bei starkem Wind entsteht (siehe Benötigte Infrastruktur, Kapitel Vehicle to grid (V2G)).
Desweiteren wird für Brennstoffzellen viel Platin benötigt, welches nicht ausreichend vorhanden ist [14].
Zurück zur Startseite Grüne Elektroautos
Weiterführende Informationen und Weblinks
Interessantes Video zur Herstellung von Lithium-Ionen-Akkus:
http://www.hyperraum.tv/tag/lithium-ionen-batterie/
Animation und Video zur Funktionsweise von Brennstoffzellen:
http://www.bigs.eu/images/prj/swf/bz/bz.html
http://www.wdrmaus.de/sachgeschichten/sachgeschichten/brennstoffzelle.php5
Einzelnachweise
- ↑ M. Lienkamp, Elektromobilität. Berlin, Heidelberg: Springer Berlin Heidelberg, 2012.
- ↑ M. Lienkamp, Elektromobilität. Berlin, Heidelberg: Springer Berlin Heidelberg, 2012.
- ↑ “Batterien fürs Elektroauto: Hab’ den Wagen voll geladen . . .,” FAZ, 2009. [Online]. Available: http://www.faz.net/aktuell/wissen/physik-chemie/batterien-fuers-elektroauto-hab-den-wagen-voll-geladen-1757956.html. [Accessed: 05-Jan-2014].
- ↑ G. Kickelbick, Chemie für Ingenieure. Pearson Deutschland GmbH, 2008, p. 407.
- ↑ M. Lienkamp, Elektromobilität. Berlin, Heidelberg: Springer Berlin Heidelberg, 2012.
- ↑ M. Lienkamp, Elektromobilität. Berlin, Heidelberg: Springer Berlin Heidelberg, 2012.
- ↑ M. Lienkamp, Elektromobilität. Berlin, Heidelberg: Springer Berlin Heidelberg, 2012.
- ↑ “Automatisierte Anlagen für das Recycling von Elektroschrott - Trenntechnik – Fertigungsautomatisierung.” [Online]. Available: https://wiki.zimt.uni-siegen.de/fertigungsautomatisierung/index.php/Automatisierte_Anlagen_f%C3%BCr_das_Recycling_von_Elektroschrott_-_Trenntechnik. [Accessed: 05-Jan-2014].
- ↑ K. Pudenz, “Forscher ermitteln Ökobilanz von Lithium-Ionen-Akkus für Elektroautos,” Springer für Professionals, Redaktion ATZonline.de, 2010. [Online]. Available: http://www.springerprofessional.de/forscher-ermitteln-oekobilanz-von-lithium-ionen-akkus-fuer-elektroautos-12302/3948546.html. [Accessed: 05-Jan-2014].
- ↑ K. Pudenz, “Lithium und Kupfer: Rohstoffe für den Ausbau der Elektromobilität,” Springer für Professionals, Redaktion ATZonline.de, 2010. [Online]. Available: http://www.springerprofessional.de/lithium-und-kupfer-rohstoffe-fuer-den-ausbau-der-elektromobilitaet-12161/3948388.html. [Accessed: 05-Jan-2014].
- ↑ G. Kickelbick, Chemie für Ingenieure. Pearson Deutschland GmbH, 2008, p. 407.
- ↑ M. Lienkamp, Elektromobilität. Berlin, Heidelberg: Springer Berlin Heidelberg, 2012.
- ↑ M. Lienkamp, Elektromobilität. Berlin, Heidelberg: Springer Berlin Heidelberg, 2012.
- ↑ M. Lienkamp, Elektromobilität. Berlin, Heidelberg: Springer Berlin Heidelberg, 2012.